What do we smelt?
The foundry input material is a fine and homogeneous ash. It is the result of a prior treatment that led to the production of a homogeneous material with a maximum particle size of 80 mesh. At this stage, the ash consists of different amounts of precious metals, non-noble metals and non-metallic materials in different concentrations.
The foundry is also able to process materials stemming from other processes, such as metals for conditioning, sludge and matte.
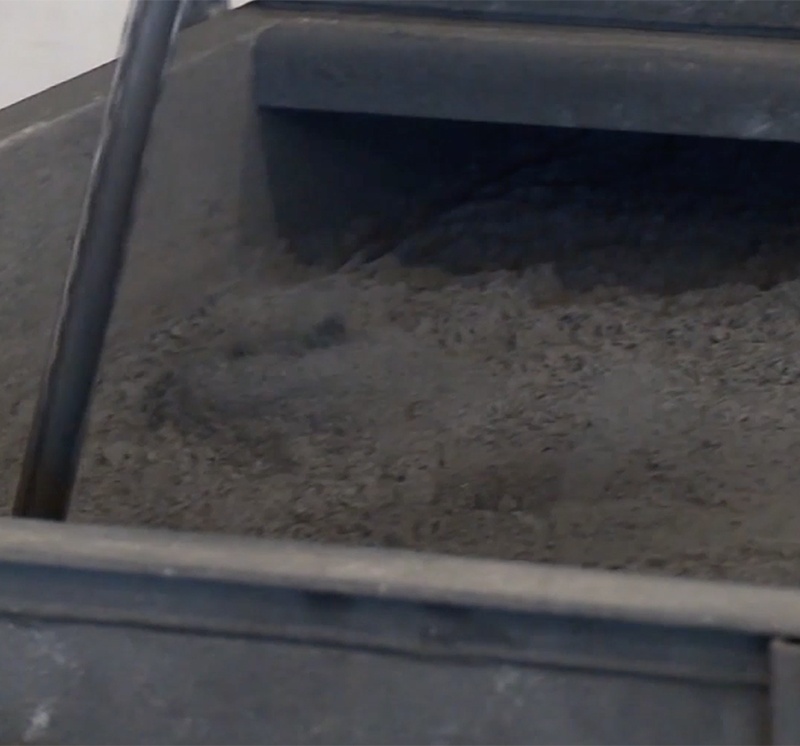
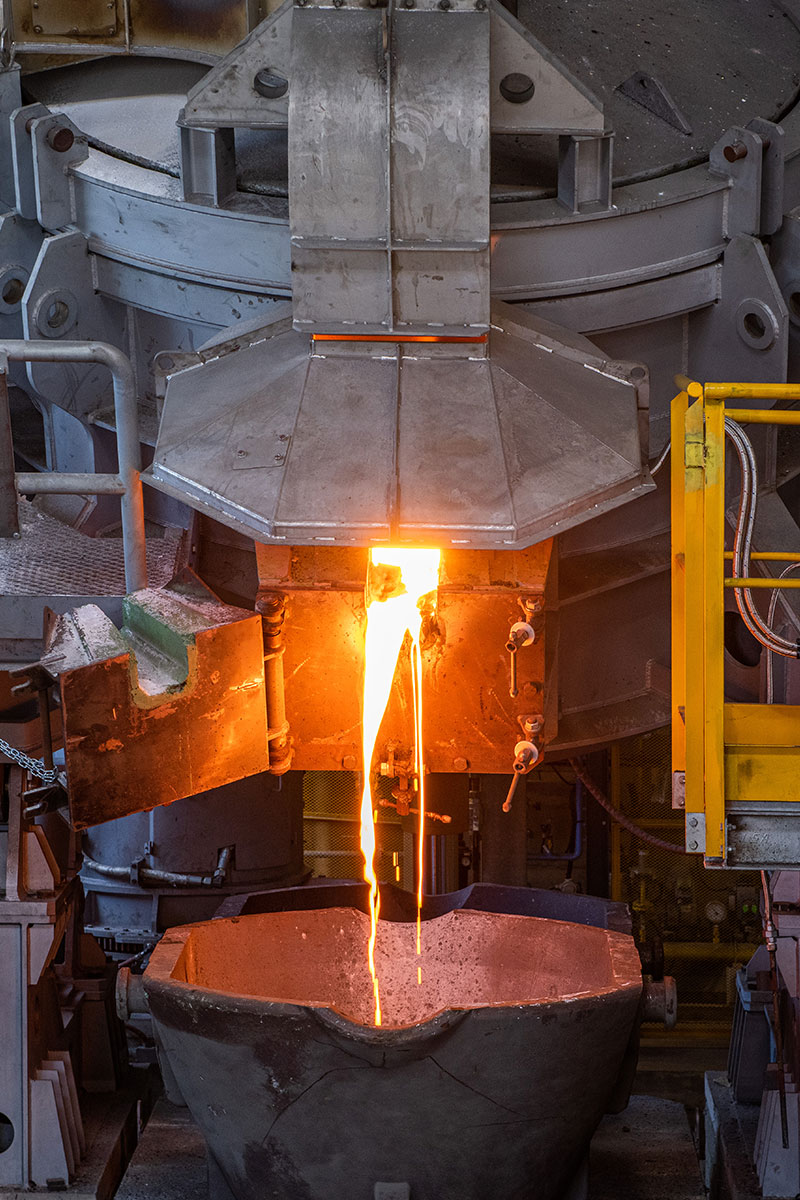